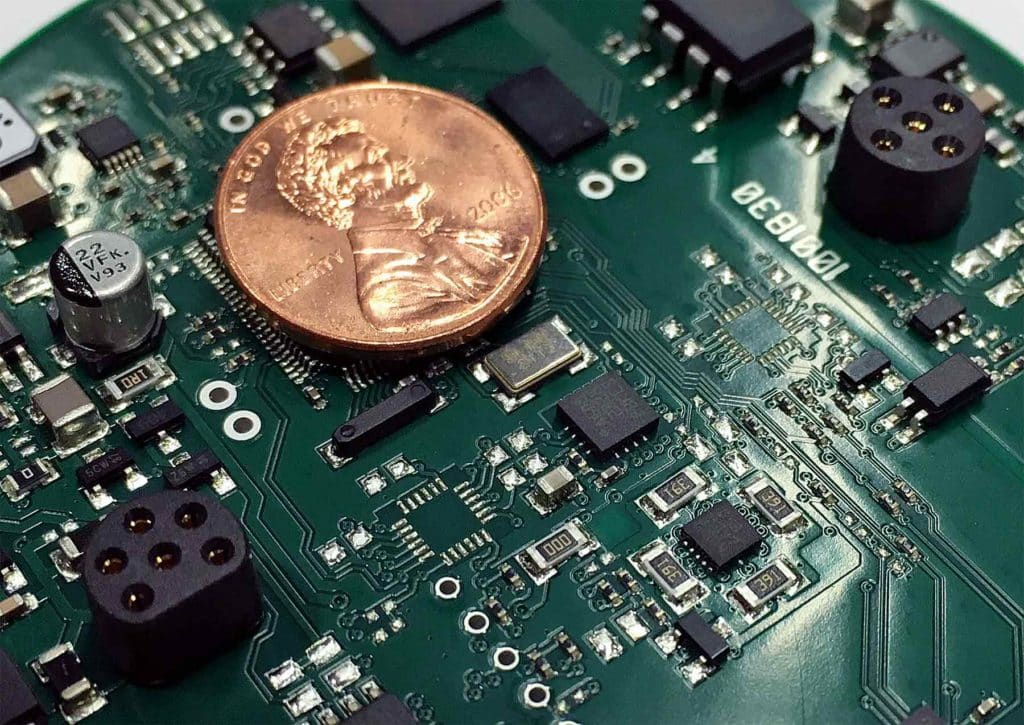
Did you know that there’s a tiny little gyroscope in your smartphone? Your drone has one too.
That gyro enables stable flight for copters and allows your phone screen to rotate. Now, that miniature motion sensor can be found in the newest 3D sonar transducers, enabling stabilized, more realistic bottom returns.
“It’s smaller than a pinkie nail,” says Jim McGowan, Raymarine’s marketing manager. “The challenge we have for measuring anything with 3D — whether sound energy or radar — is having a steady reference point to measure from.”
By Definition
For Raymarine’s new RealVision 3D and Furuno’s DFF-3D sonar units, both introduced in 2017, and for Garmin’s Panoptix all-seeing sonar, which debuted in 2016, that has meant adding a tiny gyro to the transducer. Raymarine calls this an AHRS, or attitude heading reference system; the company first used it in Evolution autopilots, starting in 2013.
Furuno calls it an MEMS motion sensor; MEMS stands for micro-electromechanical system. Garmin explains that MEMS is the sensor and AHRS includes the sensor and the software algorithms.
Because this is somewhat-new-to-sonar technology, I found the lay explanations of its characteristics to be less standard than more common systems. As it becomes widely used, I expect to see more uniform descriptions.
The gyro sensor is one way to enable proper 3D operation. But the sensor is also capable of stabilizing a traditional 2D sonar return as well. That means seeing an accurate rendering of the ocean bottom without the sawtooth effect often caused when waves make a boat pitch in heavy seas.
Technically, this is good news for offshore saltwater fishermen, who might have noticed that rough ocean conditions distort traditional and also imaging sonar returns. Such garbled targets make it tough to see the sometimes subtle details of structure that can greatly enhance fishing success.
“This is a chip that can sense motion,” says Eric Kunz, Furuno senior product manager. “No more fluid mediums. It’s all done by cutting the silicon and making chips in such a way that the silicon floats inside the chip.”
The gyro is essentially a nine-axis compass, McGowan says. So it senses movement in nine different directions, including measuring pitch, roll and yaw. McGowan went on to clarify that Raymarine has not yet enabled the sensor to eliminate sawtooth returns on 2D sonar (only for 3D), but he anticipates that capability.
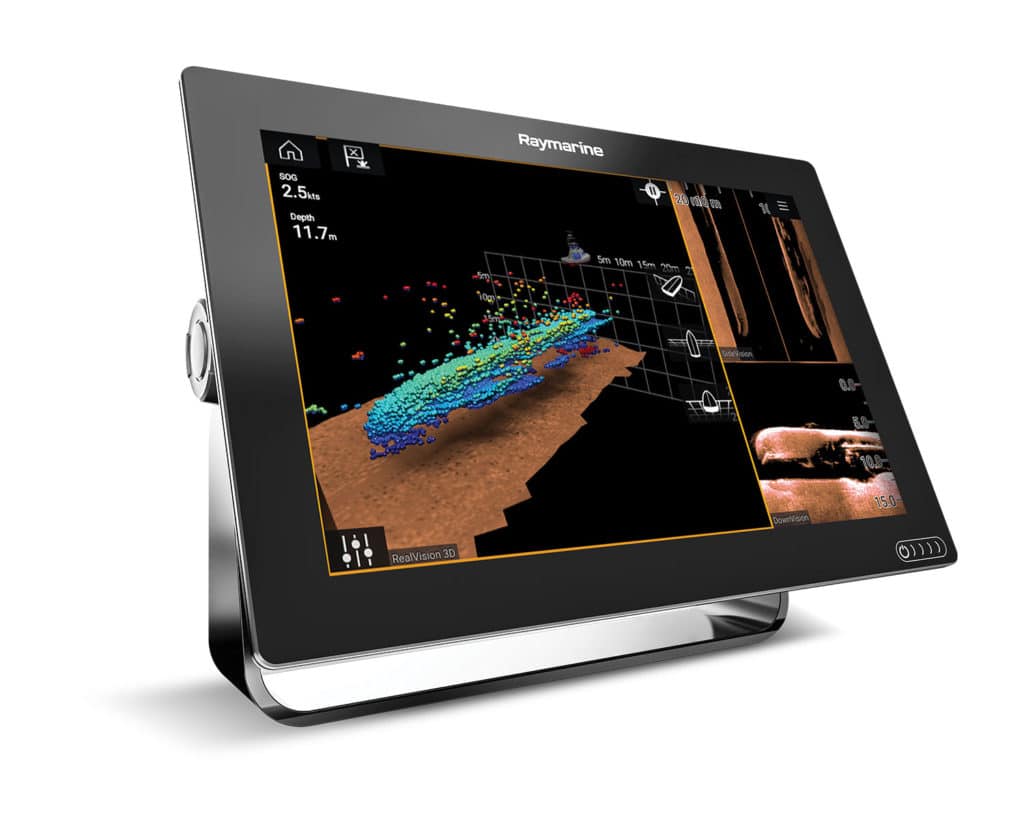
Heave-Ho
Furuno has offered what it calls heave compensation as an option for recreational sonars since it first introduced NavNet 3D display systems in 2007. Heave is caused when a boat vertically rises and falls, which also produces sawtooth bottom returns.
However, Kunz says heave compensation has always required an SC30 satellite compass ($2,495) mounted on a hardtop, connecting to the sonar and employing a vertical rate accelerometer. Once properly aligned, the system returns an accurate image of the ocean bottom — stable enough to see even the slightest structure or trough in any kind of seas.
“Our commercial products have had that for a long time,” Kunz says. “When you’re looking out 1,000 meters and you have your beam shooting out horizontally from under the boat, it’s super important to have heave compensation.”
Read Next: Find Fish with 3D, Live Sonar and All-Around Imaging
Now that MEMS sensors have dropped in price with their widespread generic electronic use, they can be placed affordably inside a transducer. The need for compensation mostly disappears with the sensor located that low in relation to the vessel structure.
Furuno’s DFF-3D multibeam sonar system employs MEMS in its transducer. The DFF-3D module is compatible with TZtouch and TZtouch2 multifunction displays.
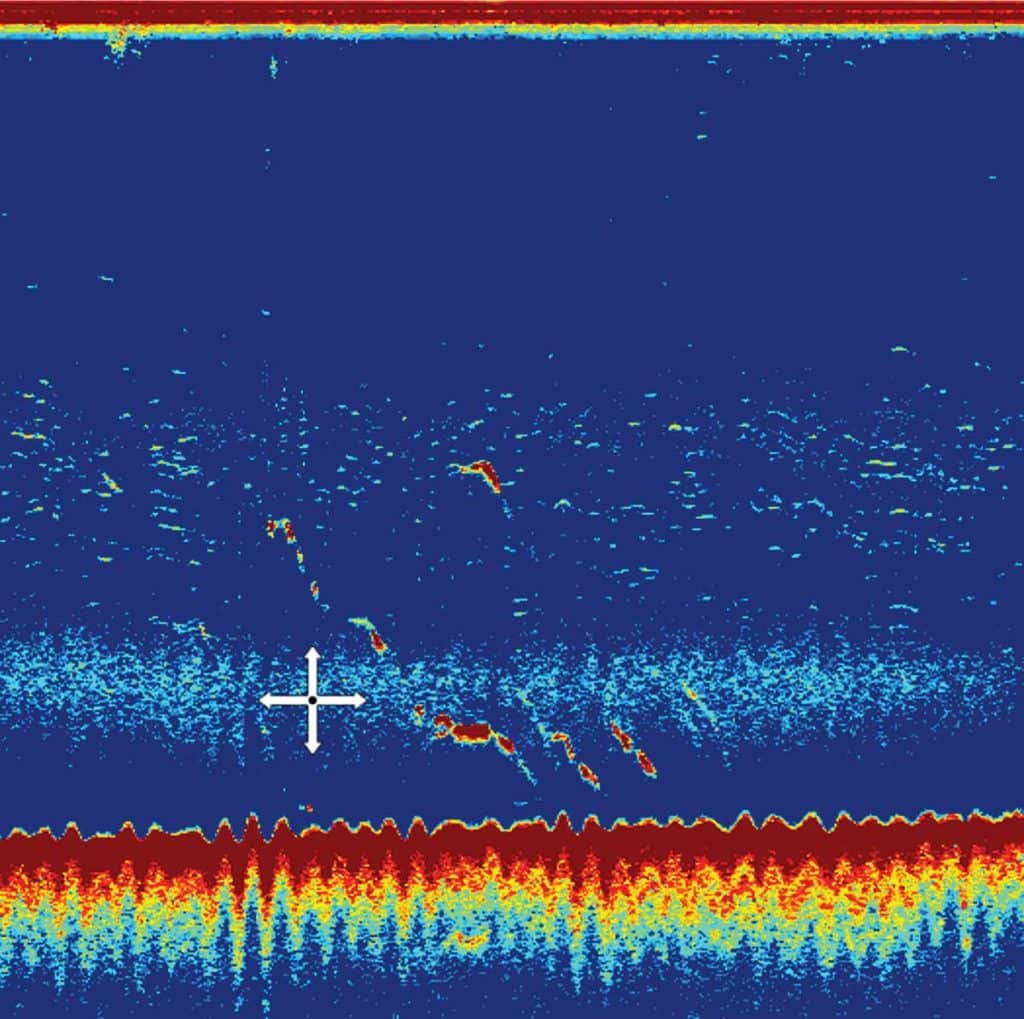
Laser Precision
For 3D sonar, MEMS sensors help deliver very precise pictures of what’s below the boat. McGowan likens the AHRS measuring process to that used by WeatherTech, makers of custom floor mats for vehicles.
“There’s a commercial on TV for WeatherTech floor mats. They do a laser scan of every vehicle so that the mats fit edge to edge,” he says. “They put a laser sensor in the footwell, and it spins around and takes all the measurements. 3D scanning works so well when it’s measuring from a fixed point.”
Raymarine has taken that technology and applied it to the sonar world, he says. “Instead of a laser light, we’re using finely focused sound energy. The trick is: The boat is always moving. So to get a really accurate 3D presentation, we need to create that reference point in the absence of true stability. We do that with the gyro sensor.”
For all practical purposes, the gyro reports in real time. With algorithms, engineers can remove the vessel motion from the image.
RealVision 3D is available in Axiom and Axiom Pro units. In settings, users can turn on or off the stabilization. “Though I don’t know why you’d want it off,” McGowan says.
I have to agree. For 3D sonar returns within these systems, it’s obviously vital. But I’d like to see it in traditional sonar. Some anglers might feel they’re not missing much when heavy seas distort bottom returns, but I would prefer as clear a picture as possible — in any conditions.